#189074 - 07/18/20 05:26 AM
Re: Abuse, faulty blade, or a combination?
[Re: Leatherman]
|
Knife Enthusiast
Registered: 09/25/13
Posts: 1219
Loc: the other side of the earth
|
I have a friend, he works as a flaw detector, I told him about this story, he immediately offered to make an examination, it looks like this picture - the product must be cleaned, then it is poured with a special agent and placed in a magnetic field - all microcracks and similar traces will be visible under ultraviolet light, including those that are in the thickness of the metal and are not visible from the outside. Here is an example of what it looks like on a steel shaft that has been hardened and then finely grinding after hardening. cracks are either a problem with improper hardening or improper cooling during the last grinding (no coolant) 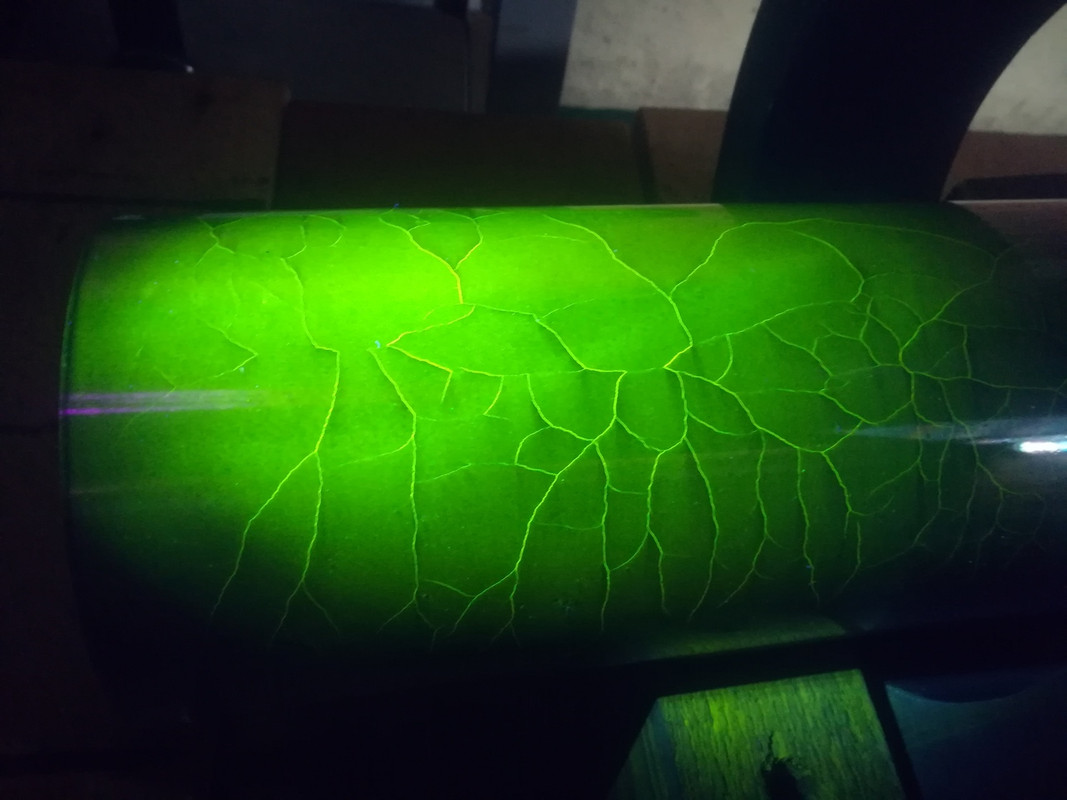 Today I talked with a friend again, it turned out to be magnetic particle inspection - https://www.youtube.com/watch?v=qpgcD5k1494there is also an interesting ultrasonic method, but I have not used this yet https://www.youtube.com/watch?v=UM6XKvXWVFAIMHO If on sergeant are no traces of these hidden defects in the fracture region, then this may be too hard metal with a thin thickness, i.e. fragile in itself, if hardness is within normal limits for O1 - 55-59 HRC **, then this is a clear abuse of instrument  I conducted such an examination of my Randall 10-5(7) [[ I bought it as 10-5, but then it turned out that it was broken off 10-7 and then re-sharpened]], no defects, unfortunately we did not take a photo at that moment, 53-54 HRC, great knife, I use it constantly. ** I don't remember what numbers were given for the Randalls, these figures are what my friend uses in his work with this steel for knives, i.e. it can be hardened up to 65 HRC, but this is only used in industrial equipment, where the load vectors are accurate and calculated for a specific structure, if you make such a knife for a person, it will most likely quickly break, unless it's a thin chef's knife that is used carefully.
_________________________
Si vis pacem, para bellum
|
Top
|
|
|
|
Abuse, faulty blade, or a combination?
|
crutchtip
|
05/13/20 01:10 PM
|
Re: Abuse, faulty blade, or a combination?
|
pappy19
|
05/13/20 01:17 PM
|
Re: Abuse, faulty blade, or a combination?
|
LarryWW1246
|
05/13/20 01:24 PM
|
Re: Abuse, faulty blade, or a combination?
|
crutchtip
|
05/13/20 01:52 PM
|
Re: Abuse, faulty blade, or a combination?
|
LarryWW1246
|
05/13/20 02:23 PM
|
Re: Abuse, faulty blade, or a combination?
|
Leatherman
|
05/13/20 03:42 PM
|
Re: Abuse, faulty blade, or a combination?
|
crutchtip
|
05/13/20 05:01 PM
|
Re: Abuse, faulty blade, or a combination?
|
Wally
|
05/13/20 05:13 PM
|
Re: Abuse, faulty blade, or a combination?
|
Windsor
|
05/13/20 05:30 PM
|
Re: Abuse, faulty blade, or a combination?
|
Chief
|
05/13/20 05:43 PM
|
Re: Abuse, faulty blade, or a combination?
|
Captain Chris Stanaback
|
05/13/20 05:52 PM
|
Re: Abuse, faulty blade, or a combination?
|
Michael_Mason
|
05/13/20 07:22 PM
|
Re: Abuse, faulty blade, or a combination?
|
Buck Buchanan
|
05/13/20 07:26 PM
|
Re: Abuse, faulty blade, or a combination?
|
Windsor
|
05/13/20 07:41 PM
|
Re: Abuse, faulty blade, or a combination?
|
crutchtip
|
05/13/20 07:44 PM
|
Re: Abuse, faulty blade, or a combination?
|
tunefink
|
05/13/20 07:53 PM
|
Re: Abuse, faulty blade, or a combination?
|
Leatherman
|
05/13/20 08:37 PM
|
Re: Abuse, faulty blade, or a combination?
|
LarryWW1246
|
05/13/20 08:56 PM
|
Re: Abuse, faulty blade, or a combination?
|
crutchtip
|
05/13/20 09:00 PM
|
Re: Abuse, faulty blade, or a combination?
|
tunefink
|
05/13/20 09:42 PM
|
Re: Abuse, faulty blade, or a combination?
|
crutchtip
|
05/13/20 09:58 PM
|
Re: Abuse, faulty blade, or a combination?
|
Sharpi
|
05/13/20 10:39 PM
|
Re: Abuse, faulty blade, or a combination?
|
pappy19
|
05/14/20 12:14 AM
|
Re: Abuse, faulty blade, or a combination?
|
Duke
|
05/14/20 02:21 AM
|
Re: Abuse, faulty blade, or a combination?
|
desert.snake
|
05/14/20 05:26 AM
|
Re: Abuse, faulty blade, or a combination?
|
rigid54
|
05/14/20 06:27 AM
|
Re: Abuse, faulty blade, or a combination?
|
Sphinx3000
|
05/14/20 07:36 AM
|
Re: Abuse, faulty blade, or a combination?
|
crutchtip
|
05/14/20 08:16 AM
|
Re: Abuse, faulty blade, or a combination?
|
Sphinx3000
|
05/14/20 08:38 AM
|
Re: Abuse, faulty blade, or a combination?
|
crutchtip
|
05/14/20 10:11 AM
|
Re: Abuse, faulty blade, or a combination?
|
Sphinx3000
|
05/14/20 10:40 AM
|
Re: Abuse, faulty blade, or a combination?
|
crutchtip
|
05/14/20 11:32 AM
|
Re: Abuse, faulty blade, or a combination?
|
Captain Chris Stanaback
|
05/14/20 12:32 PM
|
Re: Abuse, faulty blade, or a combination?
|
Eric
|
05/14/20 01:02 PM
|
Re: Abuse, faulty blade, or a combination?
|
CrazyCajun
|
05/14/20 01:16 PM
|
Re: Abuse, faulty blade, or a combination?
|
rigid54
|
05/14/20 01:20 PM
|
Re: Abuse, faulty blade, or a combination?
|
crutchtip
|
05/14/20 01:27 PM
|
Re: Abuse, faulty blade, or a combination?
|
Chief
|
05/14/20 05:01 PM
|
Re: Abuse, faulty blade, or a combination?
|
Leatherman
|
05/14/20 06:01 PM
|
Re: Abuse, faulty blade, or a combination?
|
Dirty_Water
|
05/14/20 06:17 PM
|
Re: Abuse, faulty blade, or a combination?
|
BOB_TEATES
|
05/14/20 08:06 PM
|
Re: Abuse, faulty blade, or a combination?
|
pappy19
|
05/14/20 08:13 PM
|
Re: Abuse, faulty blade, or a combination?
|
Peter_Kaufman
|
05/14/20 08:14 PM
|
Re: Abuse, faulty blade, or a combination?
|
Leatherman
|
05/14/20 09:22 PM
|
Re: Abuse, faulty blade, or a combination?
|
crutchtip
|
05/14/20 07:58 AM
|
Re: Abuse, faulty blade, or a combination?
|
Wally
|
05/15/20 02:04 AM
|
Re: Abuse, faulty blade, or a combination?
|
Sphinx3000
|
05/15/20 04:13 AM
|
Re: Abuse, faulty blade, or a combination?
|
Sphinx3000
|
05/15/20 04:16 AM
|
Re: Abuse, faulty blade, or a combination?
|
Sphinx3000
|
05/15/20 04:29 AM
|
Re: Abuse, faulty blade, or a combination?
|
Dirty_Water
|
05/15/20 05:43 AM
|
Re: Abuse, faulty blade, or a combination?
|
Sphinx3000
|
05/15/20 06:13 AM
|
Re: Abuse, faulty blade, or a combination?
|
crutchtip
|
05/15/20 07:37 AM
|
Re: Abuse, faulty blade, or a combination?
|
Sphinx3000
|
05/15/20 08:16 AM
|
Re: Abuse, faulty blade, or a combination?
|
crutchtip
|
05/15/20 08:58 AM
|
Re: Abuse, faulty blade, or a combination?
|
Sphinx3000
|
05/15/20 09:46 AM
|
Re: Abuse, faulty blade, or a combination?
|
LarryWW1246
|
05/15/20 09:54 AM
|
Re: Abuse, faulty blade, or a combination?
|
BOB_TEATES
|
05/15/20 12:03 PM
|
Re: Abuse, faulty blade, or a combination?
|
Captain Chris Stanaback
|
05/15/20 08:23 PM
|
Re: Abuse, faulty blade, or a combination?
|
spark42
|
05/15/20 11:56 PM
|
Re: Abuse, faulty blade, or a combination?
|
rigid54
|
05/16/20 12:54 PM
|
Re: Abuse, faulty blade, or a combination?
|
Doug74
|
05/16/20 02:32 PM
|
Re: Abuse, faulty blade, or a combination?
|
Chief
|
05/16/20 03:45 PM
|
Re: Abuse, faulty blade, or a combination?
|
Windsor
|
05/16/20 07:32 PM
|
Re: Abuse, faulty blade, or a combination?
|
LarryWW1246
|
05/16/20 07:39 PM
|
Re: Abuse, faulty blade, or a combination?
|
pappy19
|
05/17/20 12:03 AM
|
Re: Abuse, faulty blade, or a combination?
|
BladesNBarrels
|
05/17/20 11:05 AM
|
Re: Abuse, faulty blade, or a combination?
|
TonyLaPetri
|
05/18/20 10:00 AM
|
Re: Abuse, faulty blade, or a combination?
|
LarryWW1246
|
05/18/20 12:57 PM
|
Re: Abuse, faulty blade, or a combination?
|
TonyLaPetri
|
05/18/20 04:18 PM
|
Re: Abuse, faulty blade, or a combination?
|
Leatherman
|
05/19/20 11:49 PM
|
Re: Abuse, faulty blade, or a combination?
|
desert.snake
|
07/18/20 05:26 AM
|
Re: Abuse, faulty blade, or a combination?
|
Kirko
|
07/18/20 03:45 PM
|
Re: Abuse, faulty blade, or a combination?
|
crutchtip
|
07/19/20 01:19 PM
|
Re: Abuse, faulty blade, or a combination?
|
Tom Vaught
|
05/14/20 08:34 PM
|
Re: Abuse, faulty blade, or a combination?
|
Chief
|
05/14/20 09:22 PM
|
Re: Abuse, faulty blade, or a combination?
|
crutchtip
|
05/14/20 09:32 PM
|
Re: Abuse, faulty blade, or a combination?
|
Eric
|
05/13/20 03:50 PM
|
Re: Abuse, faulty blade, or a combination?
|
Ronnie
|
05/13/20 04:03 PM
|
Re: Abuse, faulty blade, or a combination?
|
Michael_Mason
|
05/15/20 06:52 AM
|
|
|
|